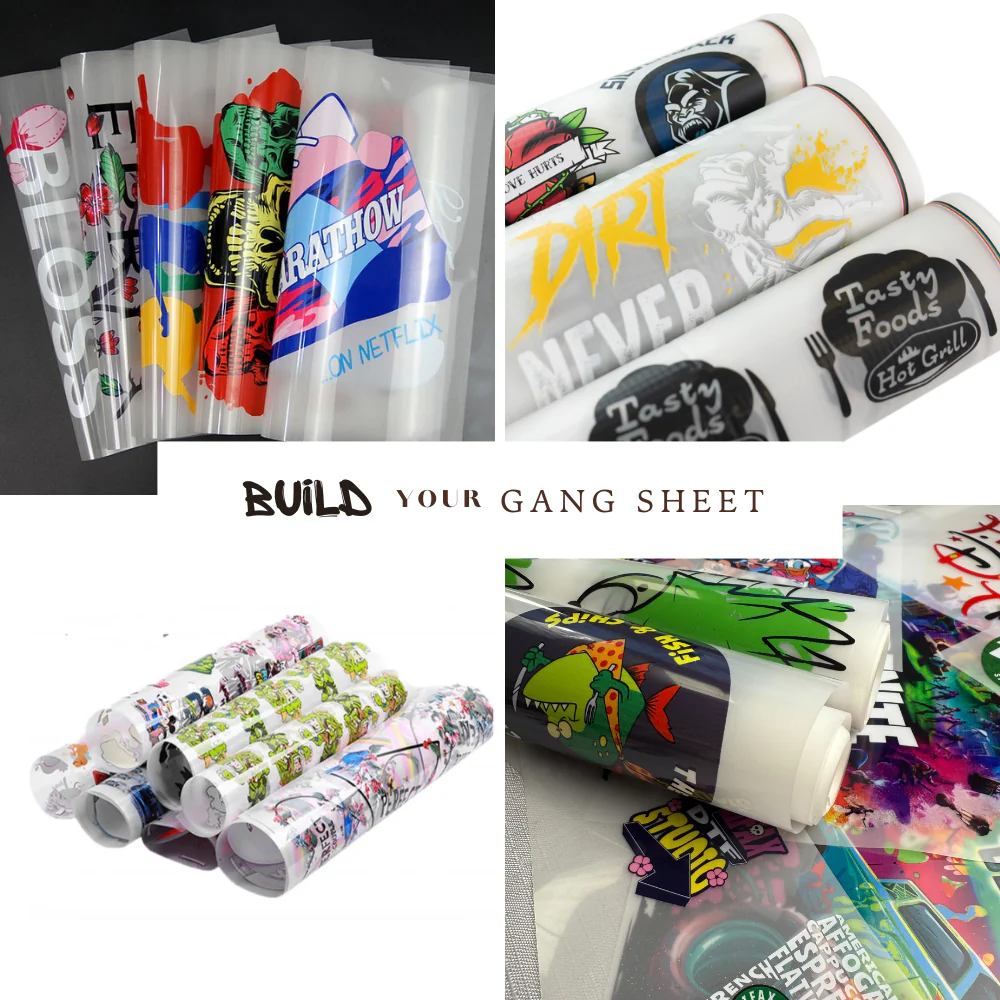
Introduction
Direct-to-Film (DTF) printing has revolutionized the custom apparel industry with its versatility and high-quality transfers. Among the essential concepts in DTF printing is the “gang sheet” – a technique that maximizes efficiency and reduces waste. This article explores everything you need to know about gang sheets for DTF printing, from basic concepts to advanced applications.
What is a Gang Sheet in DTF Printing?
A gang sheet in DTF printing refers to a single film sheet containing multiple designs arranged together for simultaneous printing. Rather than printing individual designs on separate sheets, a gang sheet combines several images on one sheet, optimizing the use of materials and printing time.
Key Features of Gang Sheets
- Space Optimization: Multiple designs are arranged to use the maximum available area of the film
- Cost Efficiency: Reduces film, powder, and ink consumption
- Time-Saving: Processes multiple designs in a single print and cure cycle
- Batch Processing: Ideal for printing diverse designs in smaller quantities
Benefits of Using Gang Sheets for DTF Printing
Material Conservation
Gang sheets significantly reduce material waste by utilizing areas of the film that would otherwise remain unused. For small businesses and print shops, this translates to considerable cost savings on film, powder, and ink over time.
Production Efficiency
By printing multiple designs simultaneously, gang sheets streamline the production workflow. Instead of setting up and processing individual transfers separately, operators can prepare, print, and cure several designs at once.
Versatility for Small Orders
Gang sheets are particularly valuable for businesses that handle numerous small orders. Rather than dedicating entire sheets to single designs, operators can combine multiple client requests on one sheet, making small-batch production economically viable.
How to Create Effective Gang Sheets
Design Organization
Effective gang sheets require thoughtful arrangement of designs. Consider these factors:
- Design Orientation: Align designs in the same direction when possible for easier powder application
- Size Variation: Combine larger designs with smaller ones to utilize space efficiently
- Spacing: Maintain adequate spacing between designs (typically 0.5-1 inch) to prevent overlap during the powder application process
Software Tools
Several design software options can help create gang sheets:
- Adobe Illustrator: Professional-grade software with precise control
- CorelDRAW: Popular for its user-friendly interface and specialized print features
- DTF-specific RIP software: Often includes gang sheet functionality with nesting capabilities
Practical Tips for Gang Sheet Creation
- Create standard templates for commonly used sizes
- Use color-coding to differentiate client orders
- Include small test patches or color samples in empty spaces
- Document your arrangements for future reference
Common Challenges and Solutions
Challenge: Powder Distribution
Problem: Uneven powder distribution across designs of varying sizes. Solution: Group designs of similar sizes together and ensure proper spacing to allow even powder distribution.
Challenge: Registration Accuracy
Problem: Difficulty aligning multi-color designs when ganged together. Solution: Include registration marks and use high-quality RIP software with precise registration capabilities.
Challenge: Film Curling
Problem: Film edges curling during the curing process. Solution: Leave adequate margins around the gang sheet perimeter and use appropriate heat settings.
Best Practices for DTF Gang Sheets
Organization Systems
Develop a consistent system for tracking designs within gang sheets:
- Use numbered positions on templates
- Implement a job tracking sheet that corresponds to gang sheet positions
- Consider QR codes or job numbers printed alongside designs
Quality Control
- Include color calibration squares on each gang sheet
- Print test transfers periodically to ensure consistent quality
- Document curing parameters for each batch
Inventory Management
- Create a digital library of commonly used gang sheet arrangements
- Track film usage to identify the most efficient layouts
- Analyze waste reduction over time to refine processes
Advanced Gang Sheet Techniques
Nested Designs
Maximizing efficiency by fitting smaller designs within the negative space of larger designs requires advanced planning but can significantly increase yield per sheet.
Variable Data Printing
Combine consistent graphic elements with changing text or numerical data (like names or numbers) across a gang sheet for team jerseys or personalized items.
Seasonal Planning
Prepare gang sheets that combine seasonal designs (holiday, sports seasons, etc.) to streamline production during peak periods.
Conclusion
Gang sheets are a vital efficiency tool in DTF printing, allowing businesses to maximize productivity while minimizing waste. By understanding proper design arrangement, overcoming common challenges, and implementing best practices, DTF print operators can significantly improve their operation’s profitability and sustainability.
Whether you’re a seasoned print shop or new to DTF technology, mastering gang sheet techniques is an essential skill that will enhance your production workflow and ultimately benefit your bottom line.
Leave a Reply